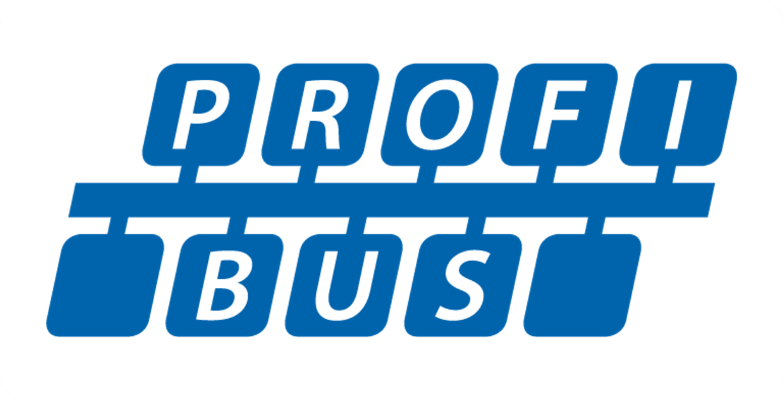
0
NodesThis 30+ year old well-established technology – and our foundation – is still widely used in various markets, with recent focus on process automation plants and areas with intrinsic safety needs. Growth continues at a moderate pace.
PROFIBUS Definition
PROFIBUS links controllers and control systems with sensors and actuators on the field level (field devices) and also enables simultaneous consistent data exchange with superordinate systems. PROFIBUS is the fieldbus-based automation standard of PROFIBUS & PROFINET International (PI). PI has also developed the PROFINET Ethernet-based automation standard and launched it successfully on the market. PROFIBUS and PROFINET use identical device profiles, thereby creating investment security and investment protection for the users and manufacturers of these technologies. Both systems cover the fields of production and process automation and therefore also enable mixed (hybrid) applications, which are often seen in the pharmaceutical, food and beverage industries.
Value Proposition
Part of the value proposition of PROFIBUS is its ability to cut costs and improve operations across the life-cycle of a plant, from design right through ongoing maintenance and even revamps. It does this in many ways: at the engineering stage it simplifies plant design, eliminates hard wiring and requires less hardware, leading to faster commissioning and lowered costs. It supports better diagnostics, making commissioning much faster. PROFIBUS also helps achieve better productivity and higher product quality through the delivery of better and more timely data to operations and management staff. In addition, it supports advanced asset management strategies for general management and maintenance.
PROFIBUS Online Training Course
For a complete introduction to PROFIBUS, consider taking this free course: us.profinet.com/profibusonline
Our course prepares students to apply PROFIBUS in their own projects. It includes technical details of the technology and a complete overview of network design, configuration, installation, commissioning, and maintenance for PROFIBUS DP and PROFIBUS PA.
History
- 1987 – the German Federal Ministry for Research and Technology requests a collaboration project called “Field Bus”. 13 companies and 5 universities jointly develop an open field bus under the name PROFIBUS, for PROcess-FIeld-BUS
- 1989 – the PROFIBUS Nutzerorganisation (PNO) is established in Germany as the first user organization
- 1992 – Switzerland establishes the second (counting PNO) Regional PROFIBUS Association (RPA), with the motto “develop globally, support locally”
- 1993 – PROFIBUS DP (Decentralized Periphery) is released and its use for discrete I/O begins
- 1994 – here in the USA, the PROFIBUS Trade Organization (PTO) is formed
- 1995 – All RPAs are pooled under the newly formed international umbrella organization PROFIBUS International (PI)
- 1996 – PROFIBUS PA (Process Automation) is created for process instruments and all related scope of applications
- 1997 – 1 million PROFIBUS devices installed
- 1999 – PROFIBUS DP is adopted as an international standard under IEC 61158
- 2000 – the first PI Competence Center (PICC) is established
- 2001 – the PROFIsafe common application profile is specified to allow for safety over logic, leveraging the establishment of PROFIBUS
- 2003 – 10 million PROFIBUS devices installed
- 2006 – the PI name is updated to include PROFINET: PI – PROFIBUS and PROFINET International
- 2009 – 30 million PROFIBUS devices installed
- 2013- over 50 million PROFIBUS devices installed
- 2014- the PNO celebrates 25 years since its foundation
- 2017- 11.5 million PROFIBUS devices in process automation systems
Fieldbuses in General
Stepping from analog to digital communication means a major paradigm shift.
In control systems that do not rely on a fieldbus, there is a clear divide between the devices and the controls; the tasks of each are separated. Only analog values (measured data) are transferred between devices and controllers, and this communication is one-way. From a personnel perspective, this typically meant that an instrumentation technologist was responsible for the field devices, and a control engineer scales the (4-20mA) analog values coming into the control system accordingly.
ISO/OSI Model
The design of the technology modules with PROFIBUS is oriented toward the ISO/OSI 7-layer model. The communication process between two nodes is distributed over seven layers, from Layer 1 (Physical Layer) to Layer 7 (Application Layer). PROFIBUS uses layers 1, 2 and 7.
Discrete Automation
Discrete -or Factory Automation- is typically characterized by faster processes than process applications. Here we use PROFIBUS DP (Decentralized Periphery). The most prevalent medium for PROFIBUS transmission is over copper wire, and for this, the easy-to-use and cost-effective RS-485 transmission technology is used. We are able to transport 244 bytes of data from 9600 bit/s up to 12 Mbit/s. This range of speeds can accommodate nearly every application. There are some instances under which wired transmission technology reaches its limits, for example in an environment with heavy interference or when bridging long distances. In these cases, optical transmission via fiber cables is available.
Process Automation
Process Automation environments, while typically requiring slower procedures, might also be characterized by explosive or hazardous environments. In such applications, we use PROFIBUS PA as opposed to PROFIBUS DP. Similarly, we can use copper wiring or fiber-optic cabling. In the case of the former, instead of RS-485, the physical layer is MBP (Manchester Encoded Bus Powered). It is important to note that even though a different physical layer is employed, PROFIBUS PA is the exact same protocol as PROFIBUS DP. MBP only transmits at one speed: 31.25 kbit/s, which is plenty for process applications. A significant departure, however, is that power and data are transported via the same cable. As such there are rules regarding network topology that must be followed.
Transmission Technologies
PROFIBUS offers flexibility in terms of transmission technology: copper-wire versions (RS485 and MBP) and optical and wireless transmission.
Topology
RS485: If RS485 transmission technology is used, all PROFIBUS field devices are typically connected in a line structure with up to 32 nodes (master and slaves) in one segment. The beginning and end of each segment are provided with active bus termination, which must be supplied with power continuously. The bus terminations are usually implemented as optionally activatable in the devices or plugs. If there are more than 32 nodes or the network span is being extended, repeaters must be used to link the networks.
Profiles
PROFIBUS Application Profiles are vendor-independent specifications implemented into PROFIBUS devices to enable the uniform behavior of devices from different manufacturers. The basic functions and services of the nodes must match to ensure smooth interaction between the bus nodes. They have to “speak the same language” and use the same concepts and data formats. This applies both for communication and for device functions and industry sector solutions. This uniformity is achieved through the use of “profiles” relating to device families or special industry sector solutions. These profiles specify features which “profile devices” must exhibit as a mandatory requirement. These can be cross-device-class features, such as safety-relevant behavior (Common Application Profiles) or device-class-specific features (Specific Application Profiles). Application Profiles are specified and maintained by PI Working Groups.
Quality Assurance and Certification
For PROFIBUS devices of different types and manufacturers to be able to perform different tasks in the automation process correctly, they must exchange information over the bus without errors. A prerequisite for this is a standard-compliant implementation of the communication protocols and application profiles by the device manufacturer. To ensure that this demand is met, PI established a quality-assurance procedure where certificates are granted for test-passing devices. Certification, assures users that PROFIBUS field devices from different manufacturers are capable of error-free operation when used together. For this purpose, the field devices are tested in practical applications in accredited independent test laboratories.
PROFIBUS Definition
PROFIBUS links controllers and control systems with sensors and actuators on the field level (field devices) and also enables simultaneous consistent data exchange with superordinate systems. PROFIBUS is the fieldbus-based automation standard of PROFIBUS & PROFINET International (PI). PI has also developed the PROFINET Ethernet-based automation standard and launched it successfully on the market. PROFIBUS and PROFINET use identical device profiles, thereby creating investment security and investment protection for the users and manufacturers of these technologies. Both systems cover the fields of production and process automation and therefore also enable mixed (hybrid) applications, which are often seen in the pharmaceutical, food and beverage industries.
Value Proposition
Part of the value proposition of PROFIBUS is its ability to cut costs and improve operations across the life-cycle of a plant, from design right through ongoing maintenance and even revamps. It does this in many ways: at the engineering stage it simplifies plant design, eliminates hard wiring and requires less hardware, leading to faster commissioning and lowered costs. It supports better diagnostics, making commissioning much faster. PROFIBUS also helps achieve better productivity and higher product quality through the delivery of better and more timely data to operations and management staff. In addition, it supports advanced asset management strategies for general management and maintenance.
PROFIBUS Online Training Course
For a complete introduction to PROFIBUS, consider taking this free course: us.profinet.com/profibusonline
Our course prepares students to apply PROFIBUS in their own projects. It includes technical details of the technology and a complete overview of network design, configuration, installation, commissioning, and maintenance for PROFIBUS DP and PROFIBUS PA.
History
- 1987 – the German Federal Ministry for Research and Technology requests a collaboration project called “Field Bus”. 13 companies and 5 universities jointly develop an open field bus under the name PROFIBUS, for PROcess-FIeld-BUS
- 1989 – the PROFIBUS Nutzerorganisation (PNO) is established in Germany as the first user organization
- 1992 – Switzerland establishes the second (counting PNO) Regional PROFIBUS Association (RPA), with the motto “develop globally, support locally”
- 1993 – PROFIBUS DP (Decentralized Periphery) is released and its use for discrete I/O begins
- 1994 – here in the USA, the PROFIBUS Trade Organization (PTO) is formed
- 1995 – All RPAs are pooled under the newly formed international umbrella organization PROFIBUS International (PI)
- 1996 – PROFIBUS PA (Process Automation) is created for process instruments and all related scope of applications
- 1997 – 1 million PROFIBUS devices installed
- 1999 – PROFIBUS DP is adopted as an international standard under IEC 61158
- 2000 – the first PI Competence Center (PICC) is established
- 2001 – the PROFIsafe common application profile is specified to allow for safety over logic, leveraging the establishment of PROFIBUS
- 2003 – 10 million PROFIBUS devices installed
- 2006 – the PI name is updated to include PROFINET: PI – PROFIBUS and PROFINET International
- 2009 – 30 million PROFIBUS devices installed
- 2013- over 50 million PROFIBUS devices installed
- 2014- the PNO celebrates 25 years since its foundation
- 2017- 11.5 million PROFIBUS devices in process automation systems
Fieldbuses in General
Stepping from analog to digital communication means a major paradigm shift.
In control systems that do not rely on a fieldbus, there is a clear divide between the devices and the controls; the tasks of each are separated. Only analog values (measured data) are transferred between devices and controllers, and this communication is one-way. From a personnel perspective, this typically meant that an instrumentation technologist was responsible for the field devices, and a control engineer scales the (4-20mA) analog values coming into the control system accordingly.
ISO/OSI Model
The design of the technology modules with PROFIBUS is oriented toward the ISO/OSI 7-layer model. The communication process between two nodes is distributed over seven layers, from Layer 1 (Physical Layer) to Layer 7 (Application Layer). PROFIBUS uses layers 1, 2 and 7.
Discrete Automation
Discrete -or Factory Automation- is typically characterized by faster processes than process applications. Here we use PROFIBUS DP (Decentralized Periphery). The most prevalent medium for PROFIBUS transmission is over copper wire, and for this, the easy-to-use and cost-effective RS-485 transmission technology is used. We are able to transport 244 bytes of data from 9600 bit/s up to 12 Mbit/s. This range of speeds can accommodate nearly every application. There are some instances under which wired transmission technology reaches its limits, for example in an environment with heavy interference or when bridging long distances. In these cases, optical transmission via fiber cables is available.
Process Automation
Process Automation environments, while typically requiring slower procedures, might also be characterized by explosive or hazardous environments. In such applications, we use PROFIBUS PA as opposed to PROFIBUS DP. Similarly, we can use copper wiring or fiber-optic cabling. In the case of the former, instead of RS-485, the physical layer is MBP (Manchester Encoded Bus Powered). It is important to note that even though a different physical layer is employed, PROFIBUS PA is the exact same protocol as PROFIBUS DP. MBP only transmits at one speed: 31.25 kbit/s, which is plenty for process applications. A significant departure, however, is that power and data are transported via the same cable. As such there are rules regarding network topology that must be followed.
Transmission Technologies
PROFIBUS offers flexibility in terms of transmission technology: copper-wire versions (RS485 and MBP) and optical and wireless transmission.
Topology
RS485: If RS485 transmission technology is used, all PROFIBUS field devices are typically connected in a line structure with up to 32 nodes (master and slaves) in one segment. The beginning and end of each segment are provided with active bus termination, which must be supplied with power continuously. The bus terminations are usually implemented as optionally activatable in the devices or plugs. If there are more than 32 nodes or the network span is being extended, repeaters must be used to link the networks.
Profiles
PROFIBUS Application Profiles are vendor-independent specifications implemented into PROFIBUS devices to enable the uniform behavior of devices from different manufacturers. The basic functions and services of the nodes must match to ensure smooth interaction between the bus nodes. They have to “speak the same language” and use the same concepts and data formats. This applies both for communication and for device functions and industry sector solutions. This uniformity is achieved through the use of “profiles” relating to device families or special industry sector solutions. These profiles specify features which “profile devices” must exhibit as a mandatory requirement. These can be cross-device-class features, such as safety-relevant behavior (Common Application Profiles) or device-class-specific features (Specific Application Profiles). Application Profiles are specified and maintained by PI Working Groups.
Quality Assurance and Certification
For PROFIBUS devices of different types and manufacturers to be able to perform different tasks in the automation process correctly, they must exchange information over the bus without errors. A prerequisite for this is a standard-compliant implementation of the communication protocols and application profiles by the device manufacturer. To ensure that this demand is met, PI established a quality-assurance procedure where certificates are granted for test-passing devices. Certification, assures users that PROFIBUS field devices from different manufacturers are capable of error-free operation when used together. For this purpose, the field devices are tested in practical applications in accredited independent test laboratories.